How Successful Design for Manufacturing Lowers Costs and Improves Quality
About 70% of your manufacturing costs for a product will emerge from decisions you make during the design phase. That is why it’s critical to practice Design for Manufacturing (DFM). The goal of DFM is to design a product that is affordable, easy to manufacture, and gives you a final product that looks and functions as expected.
Oftentimes when people move into production and realize their molded parts don’t work properly, it’s because they overlooked critical steps in DFM. Errors such as this mean longer lead times and increased costs. For example, skipping DFM may cause you to have to build an entirely new mold for your product to make sure it functions properly. Building a new mold is extremely expensive, time-consuming, and delays your product hitting the market.
Focusing on DFM early in the design phase makes the difference between a project easily moving into production or getting stuck in product development.
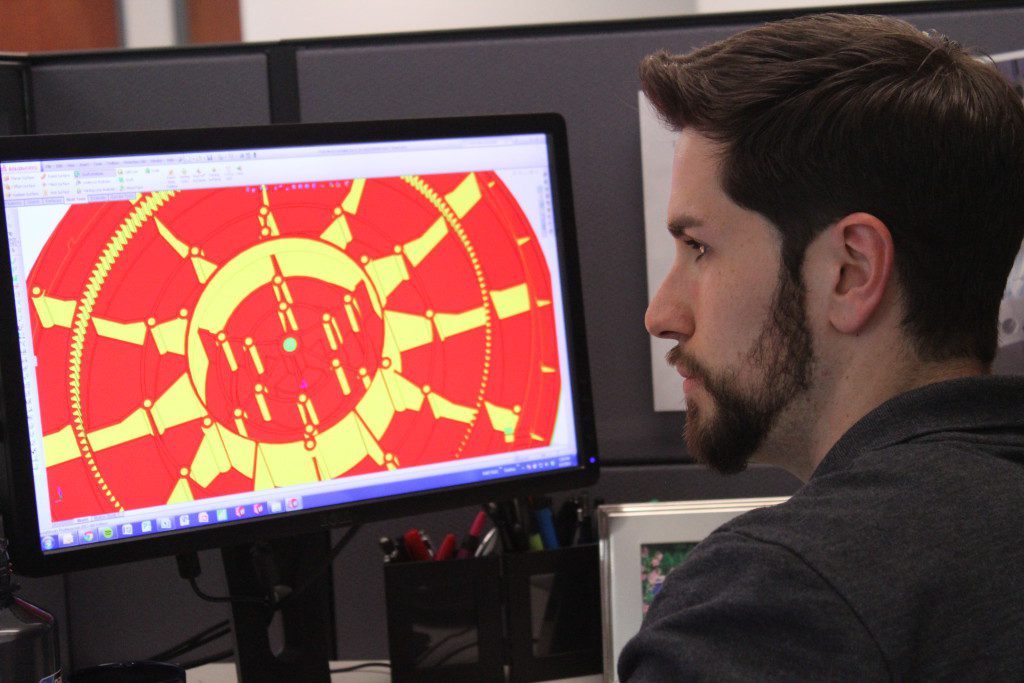
What is Design For Manufacturing?
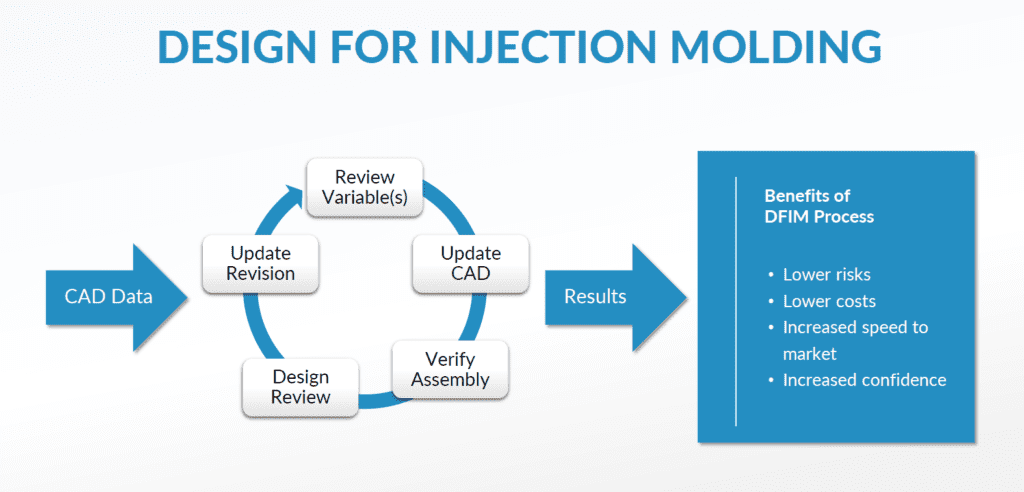
Design for Manufacture (DFM) is a crucial step in the product development process. DFM involves optimizing a part, product, or component’s design for manufacturing and assembly. Successful DFM includes reducing manufacturing costs, minimizing production and assembly complexity, and improving quality.
During DFM, all your suppliers, engineering experts, and anyone else you have engaged will help you foresee manufacturing risks and prevent them before you begin the mold. They challenge the design aspects, such as number of components in a part, part material, and surface finishes and complexity, to make sure the qualities are appropriate. Engineers will also want to consider timeline, quality, and aesthetic requirements, such as gate vestige, cycle times, and loss rate.
For example, engineers must consider a client’s aesthetic requirements and may want to avoid quality issues. They want to consider overall timeline to prevent longer cycle times. Engineers and designers should work together during DFM to anticipate these potential problems while maintaining design intent.
Why Should I Design for Manufacture?

More than half of your manufacturing costs for a product arise because of decisions made during the design phase. These decisions may include cost of materials, processing, and assembly. It is critical for DFM to happen early in the design process before molding/tooling even begins because it is difficult and expensive to make changes down the line.
Integrating Design for Manufacture during the design phase is essential for two main reasons.
1. You Will Significantly Reduce Upfront Costs
A key benefit to examining DFM during the easy design phase is reduced cost. Companies are able to reduce costs through DFM by reducing the number of part components, reducing complexity, selecting the most efficient material, and selecting the right mold and process in the beginning.
For example, multiple part components can be combined to reduce part quantity, assembly labor, and material amount. Reducing the number of product parts also reduces engineering, production, and shipping costs.
Additionally, selecting the best combination between material and fabrication process decreases manufacturing costs. You can avoid unnecessary operations such as polishing ad finishing machining to bypass higher production costs by utilizing proper DFM.
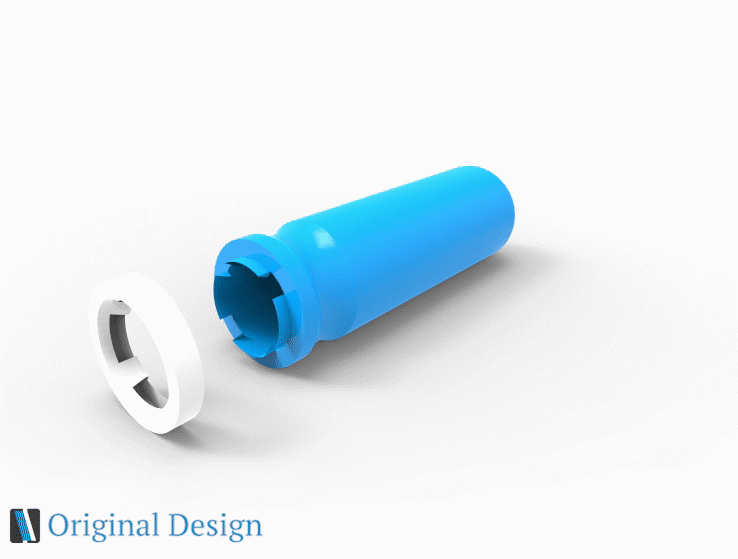
Component Reduction:
Eliminating the unnecessary component decreased the mold count, assembly operations, assembly risk, and piece price cost, saving the program over $55,000.
A medical device manufacturer needed a closed system for a sealed liquid. The original design), had two molded components. During DFM, the engineer suggested reducing the component and implementing open slots, which allowed for the creation of interlocking features within the single component for the final design.
2. You Have Greater Confidence in Your Final Product
When you begin manufacturing, you want to be certain the your part is going to consistently look and function as needed. By utilizing Design for Manufacturing during your design phase, you have greater confidence in the quality of your end product.
This is because parts can continually be updated and improved upon during design, enhancing the quality of the product. A key component of DFM is reviewing the current design and continuing to make iterations and improvements to the design until it is fully ready to be manufactured.
If you use standardized parts instead of custom-made components, it is more likely to reliably meet the same quality requirements. Because these parts are more common and available, they also reduce product lead times and save costs.
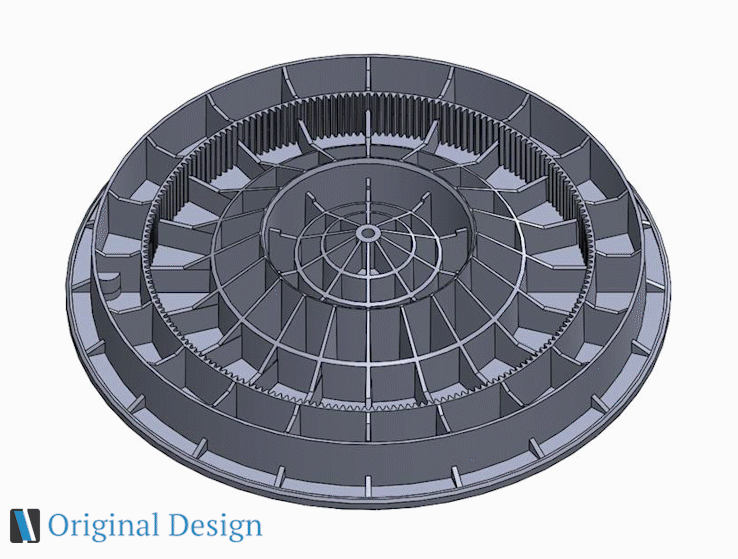
Reducing Risks by Reducing Features:
A client designed ribbing features to an electronics housing to achieve the necessary strength and flatness properties.
After a Design for Manufacturability analysis, the Natech engineers discovered the excessive ribbing posed major ejection risks. The engineers reduced the number of ribs and other features, which reduced risks and costs.
Achieving Success Through DFM
Many design firms think they know how to injection mold a part. But until you are in the trenches of designing a mold, potential risks, such as a mold breaking over time, are not as obvious. These plastic injection molding risks are obvious to our engineers because we have experience from a tooling, engineering, and manufacturing perspective.
We create realistic devices because we’ve dealt with tons of applications with similar headaches. You should work with an experienced partner that will Design for Manufacture and Design for Injection Molding so you can optimize your part design.
When clients come to Natech with their designs, we conduct a DFM analysis on the initial product design to address potential functional, operational, and financial risks. Other times, clients reach out because because they did not receive enough Design for Manufacture (DFM) support at another manufacturer.
Projects see major benefits during a thorough Design for Manufacturing analysis. Read examples of how clients have achieved success through Natech’s comprehensive DFM process.

Reducing the number of components
In a medical device, the original design includes two individual molded components. However, during DFM, engineers realized the same part requirements and functionality could be achieved by using a single component in an up and down mold. Overall, this reduced the number of molds needed, assembly operations costs, and risks.
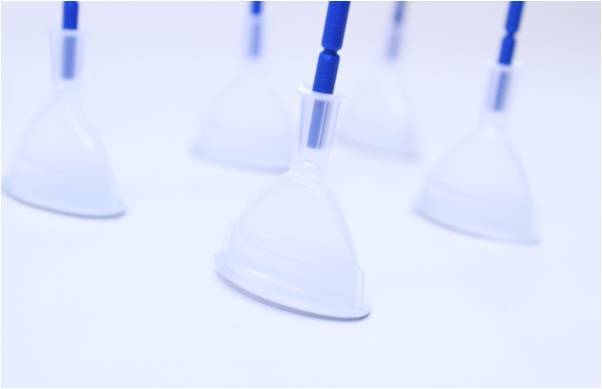
Identifying risks during the design phase
In a unit dose package, one client needed to avoid delays and costs from mold and process changes. After receiving inadequate support from another injection molder, they began to utilize Natech’s engineers and expertise to bring their product to life. By finding additional, previously unforeseen risks in the breakability and ejection of the part, they avoided major costs and risks for the future.

Product research should not only happen during initial product ideation, but also during a well-thought out DFM analysis. In this instance, Natech engineers did product research on liquid seals to pass liquid seal tests. By thoroughly investigating current opportunities, as well as historic challenges, they were able to design a component that satisfied initial product testing needs and improved user functionality.
Don’t know where to start with your project? Schedule a Design for Manufacture review with an engineer. Improve your product designs with a team that wants to help you reduce unnecessary costs and prevent quality issues.
Phone: (631) 580-3506
Email: info@natechplastics.com