Sometimes individual passion reaps organizational rewards. At the heart of injection molding lies a basic process with its own inputs and outputs. The passion for understanding the science behind that process cannot be forced, and the clients of those who have that passion can realize significant savings.
The Application
A client recently transferred a 40-mold program to Natech. One of those molds made a high impact acrylic component with a length of 392 mm (+0/-0.5 mm). This translates into a 0.1% tolerance on a part with a length-to-thickness ratio of 157:1. The client wanted it to be as close as possible to 392 mm without going over. It was to fit with a mating component, and if it were too short, it would have a loose fit. If it were too long, it would not fit at all.
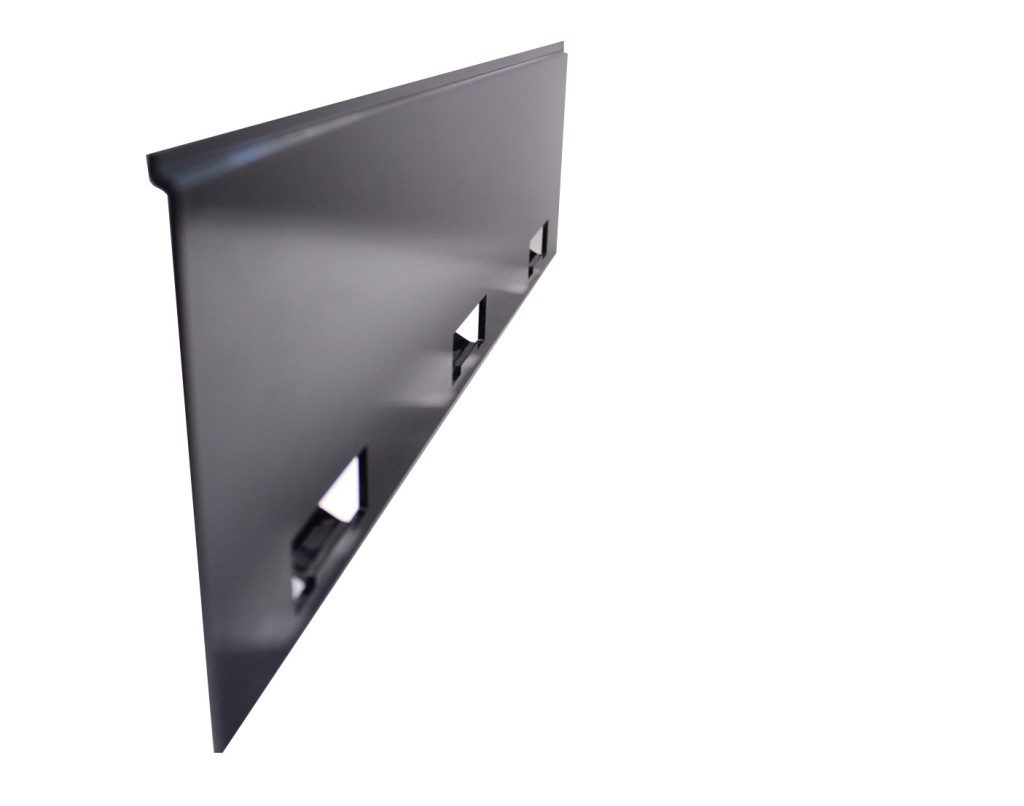
The Challenge
When Natech received the mold and sampled it, the actual dimension was 391 mm, which was below the lower tolerance of the part. The actual steel measurement of the mold was 392 mm. This meant the Moldmaker did not properly account for the shrinkage of the resin. When thermoplastics cool, they also shrink, and different resins shrink at different rates. A good moldmaker will design the mold to factor in the appropriate shrinkage rate for the resin to be used.
If the material were expected to shrink 0.3% to 0.8%, that would translate into an expected shrinkage of 1.2 mm to 3.1 mm. Making the dimension in the mold exactly the nominal did not properly factor in the shrink rate and almost guaranteed the need for an adjustment to the mold. Yes, it would have been a steel-safe change, but the moldmaker could have chosen a more accurate dimension and still remained conservative from a risk-management perspective.
Unfortunately, what was done was already done, and now the client had no time to spare and needed to get parts to their client by a hard deadline. Introducing a mold adjustment at this point would have been the knee-jerk reaction, but fortunately for this client, Natech’s engineers are passionate about and experienced in scientific molding and the supporting competencies such as Design of Experiments.
The Approach
Modifying any process can take two possible tracks. The first approach would be what has been referred to as the “Button-pushing Cowboy Approach.” In this approach, the process technician uses some combination of intuition, feel, and random creativity to adjust parameters until something either works or until they give up for whatever reason. If they get lucky enough to hit on a good shot, they usually stop there, log the parameters, and hope all future shots are just as good.
The more scientific approach involves setting up a Design of Experiments. In this approach, the process engineer predefines a set of parameters to alter, the values at which to alter them, and the various combinations necessary to paint enough of a picture to identify the impact of the variations of the variables. The engineer is essentially testing a window of possibilities to collect clues to where the real processing window resides.
The Results
Of the many controllable variables in the molding process, four variables are known to be impactful to affecting shrinkage. The Natech Engineers defined a low and high value for each variable, which gave 16 possible combinations of low and high for each variable.
Four of those 16 processes produced parts that were long enough for the part to connect properly with the mating component, and the client accepted parts from all four processes. These four processes painted a picture of the processing window. With that information, the Natech engineers had enough information to estimate the nominal process which would produce the optimized parts.
Taking a scientific approach to injection molding processes reduced cost, helped the client meet a strict deadline, and made a huge reduction in the risks. Developing the competency in the scientific approach does require an organizational commitment of time and resources, but the resulting benefits in saved costs, reduced time frames, and improved quality can more than offset that investment.